Welcome to the Kappahl Group
We are one of the leading fashion companies in the Nordic region, with over 340 stores in five countries and online sales in 30 markets. Being able to love fashion and also be part of a sustainable future is a matter of course for us. Our Kappahl and Newbie brands are underpinned by the vision to create a responsible world of fashion. Welcome to the Kappahl Group!
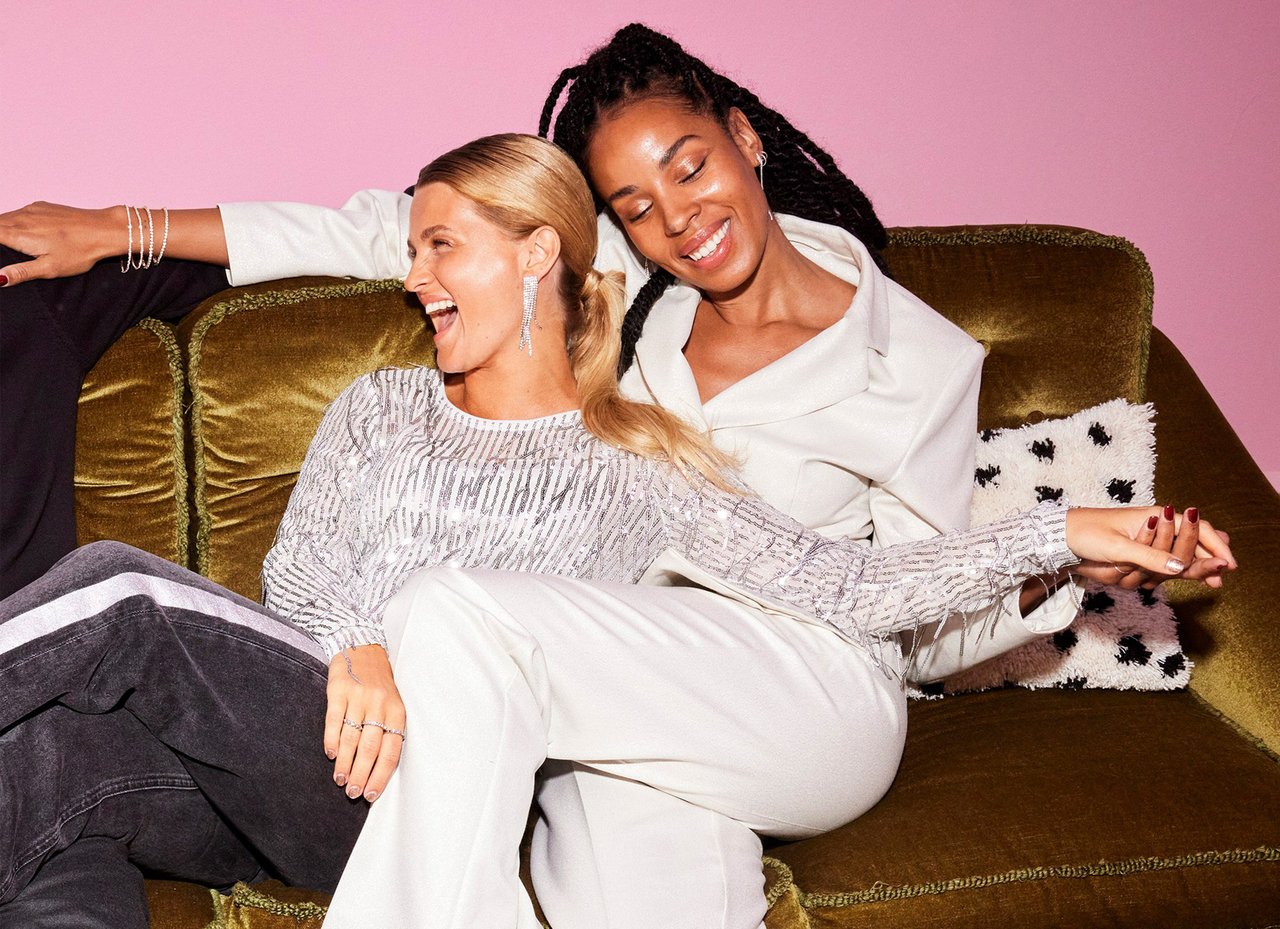
This is the Kappahl Group
We have been providing affordable and responsible fashion to millions of customers since 1953. With our Kappahl and Newbie brands, we are one of the leading fashion companies in the Nordic region.
Sustainability
Is it possible to love fashion and be part of a sustainable future at the same time? We are confident that it is!
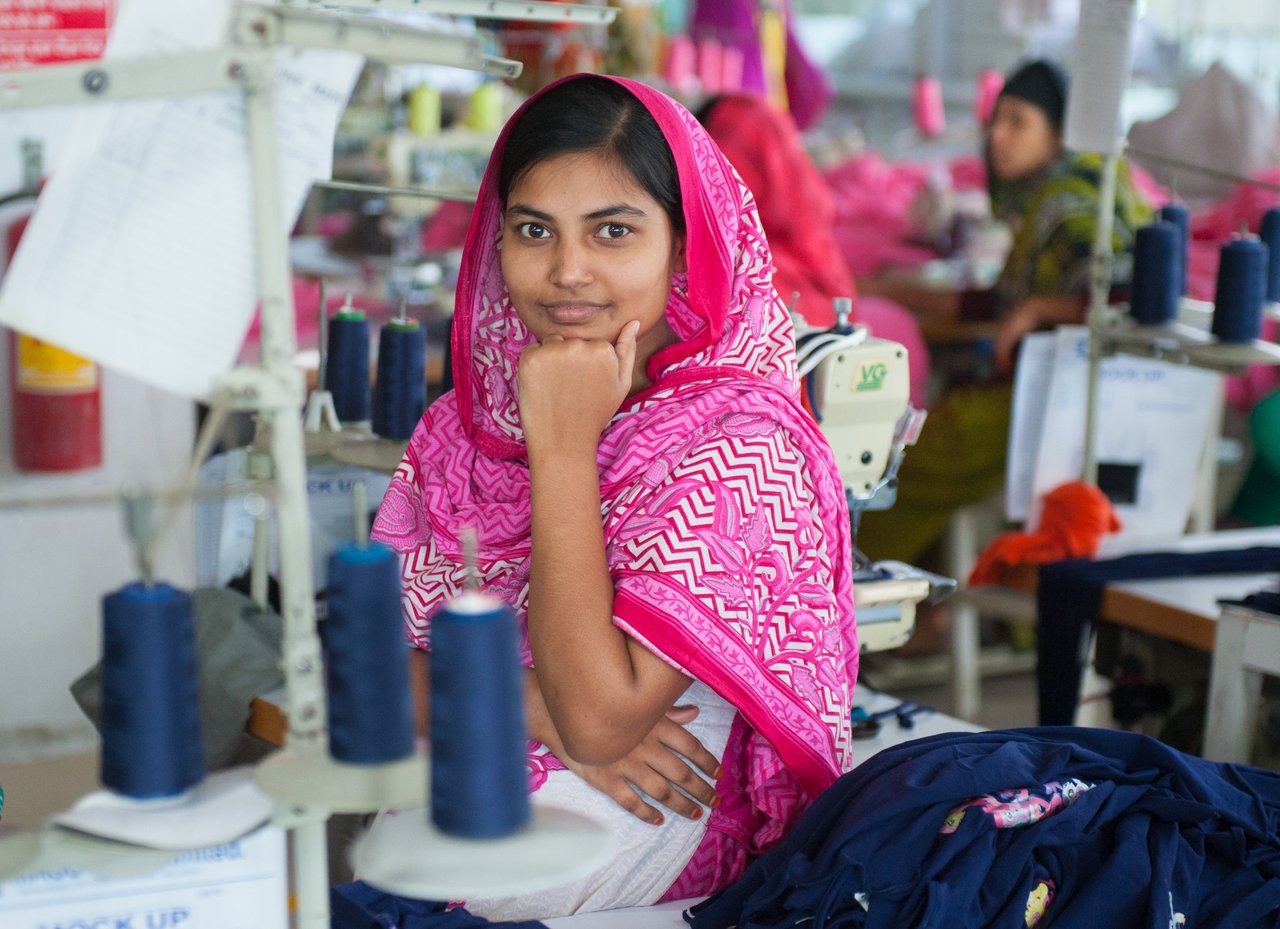
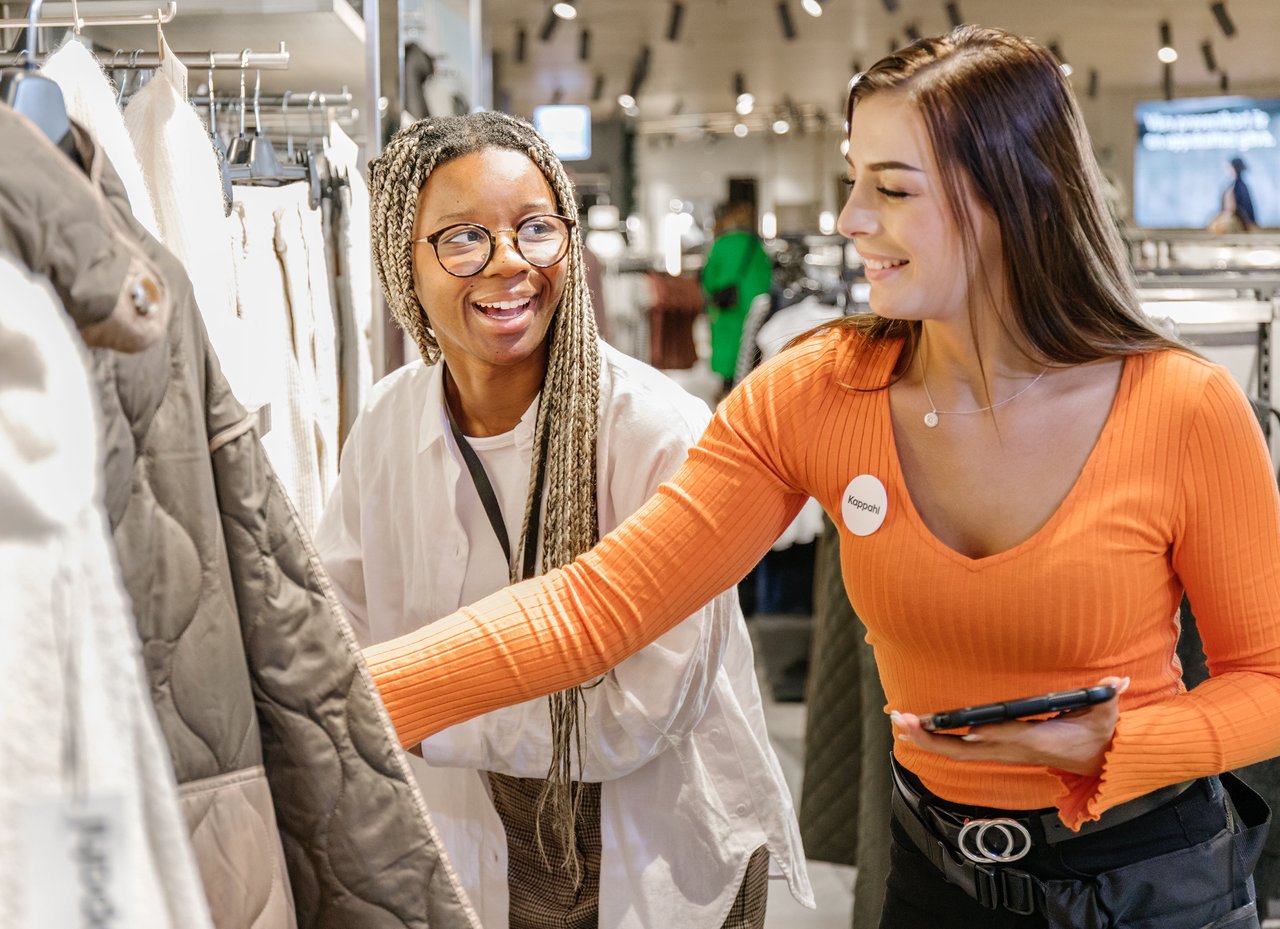
Work with us
Together we are challenging and developing the fashion industry. It’s a mission that involves a variety of roles, ranging from design and product development to warehouse and sales. You’re welcome to join us on our journey!
340+
stores in Sweden, Norway, Finland, Poland and the UK.
30+
online markets in Europe and Asia.
4,000
employees in eight countries in Europe and Asia.
Net zero
by 2040, the Kappahl Group will have net zero carbon emissions.